Modern Methods of Construction
What is MMC?
According to the MHCLG (Ministry of Housing, Communities & Local Government) Joint Industry Working Group, MMC is a range of approaches that spans off-site, near-site and on-site pre-manufacturing, process improvements and technology applications.
The MMC definition framework developed by the MHCLG describes the seven categories of MMC that enables the full and future-proofed range of “MMC” to be better understood utilising regularised terminology.
The definition framework spans all types of pre-manufacturing, site-based materials and process innovation. The term “pre-manufacturing” encompasses processes executed away from the final workforce, including in remote factories, near-site or on-site “pop-up” factories that utilise the application of a manufactured led fabrication or consolidation process in controlled conditions prior to final assembly or installation. On-site “workforce factories” are included in category 7.
The seven categories of MMC
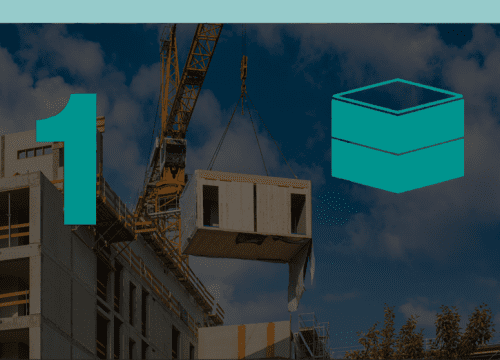
Pre-Manufacturing
(3D primary structural systems)
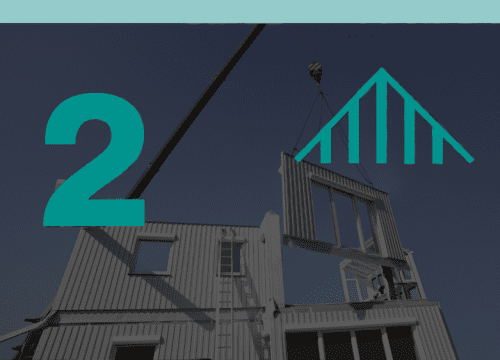
Pre-Manufacturing
(2D primary structure systems)
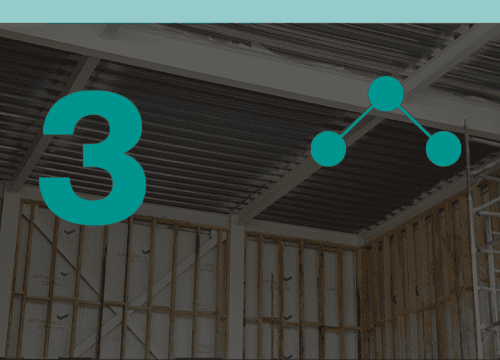
Pre-Manufacturing
(Non systemised structural components)
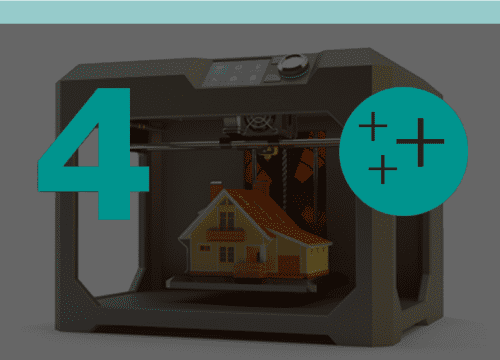
Pre-Manufacturing
(Additive manufacturing)
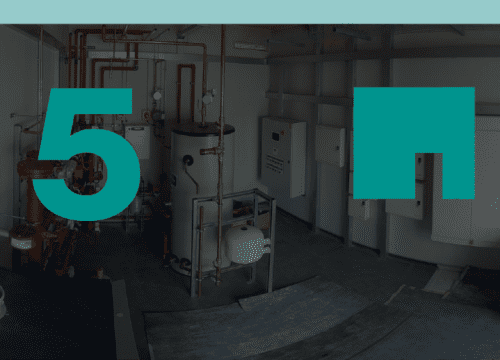
Pre-Manufacturing
(Non-structural assemblies & sub-assemblies)
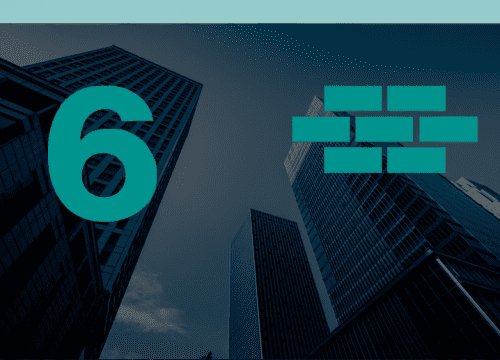
Traditional building
(Product led site labour reduction/ productivity improvements)
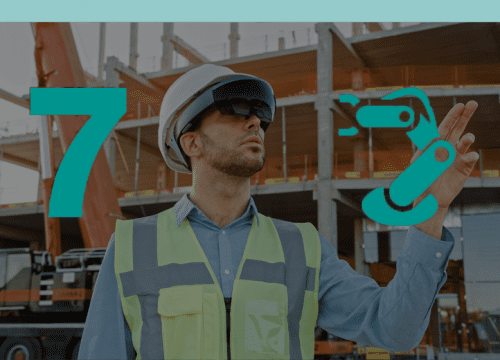
Traditional building
(Site process led labour reduction/ productivity improvements)
Category 4, additive manufacturing, relates to the 3D printing of components or whole elements of buildings. While this form of MMC is not available for use in construction projects currently, it is expected to be used in future, and so it has been included to ensure the definition framework is future-proofed.
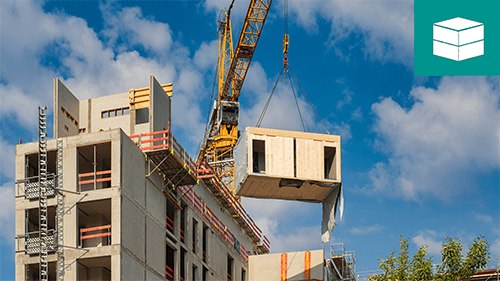
Category 1
Pre-manufacturing (3D Primary Structural Systems)
The creation of 3D structures away from site which are then combined on site to create a building. The extent of work that is carried out to the structure can vary. This is the form of MMC that incorporates the highest level of pre-manufacture, and utilises a range of core materials.
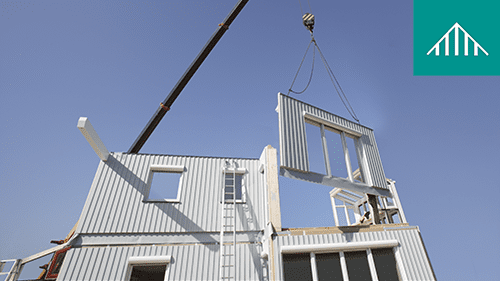
Category 2
Pre-manufactured (2D primary structural systems)
The creation of 2D panelised and framing systems away from site that are assembled on site to create the structure of a building.
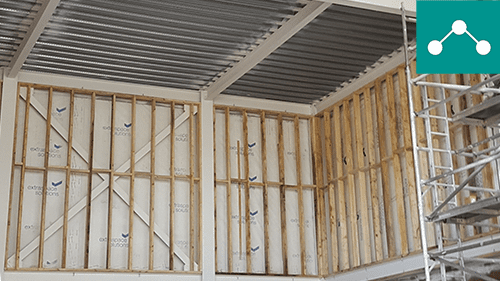
Category 3
Pre-manufactured (non-systemised primary structure)
The use of pre-manufactured components to form part of the structure of a building. These can incorporate foundation solutions as well as solutions for the main structure.
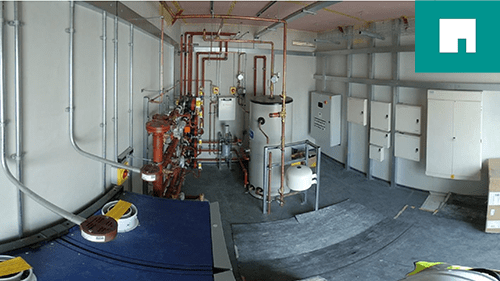
Category 5
Pre-manufacturing (non structural assemblies and sub-assemblies)
The use of pre-assembled components that do not form the structure of the building which consolidate materials and processes that otherwise would be delivered on site. These solutions can be used in isolation in an otherwise traditionally constructed project, and include commonly used items such as bathroom pods.
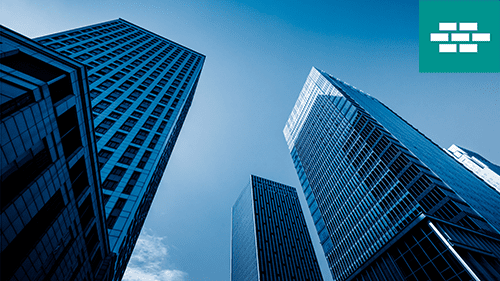
Category 6
Traditional building (product led site labour reduction / productivity improvements)
The evolution of traditional building materials so that they are quicker, easier and safer to install. This can typically involve either large format versions of traditional materials, or materials that have been developed to be easier to install with less reliance on on-site labour.
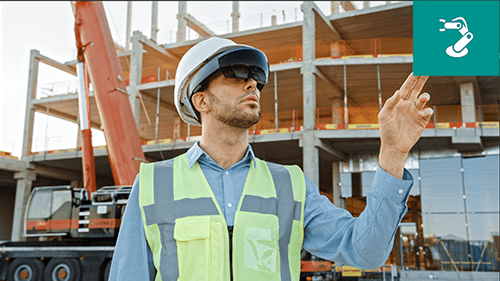
Category 7
Traditional building (site process led site labour reduction / productivity / assurance improvements)
The use of systems and processes on-site to drive productivity by removing unnecessary work stages, enabling better and faster installation and improving health and safety.
How can we help?
Our team are highly experienced in designing MEP installations within Category 1 MMC buildings, as utilised in the £3bn DfE offsite schools’ framework. We understand the relationship between the MEP installation and the modularised nature of the buildings and the need to standardise components and specify MEP components and systems that can be partially assembled and tested within the factory and connected on-site to form a complete installation.
By the nature of the materials used, MMC buildings are often lightweight in mass and can present significant challenges in complying with the DfE output specification in limiting summertime overheating. Over the years, our team have developed design techniques and MEP system specifications that overcome these challenges resulting in fully DfE compliant buildings. In extreme cases (such as where a high percentage of the façade is glazed) where MMC buildings are prone to potential overheating, we have specified phase change materials to achieve compliance without resorting to mechanical cooling, as was the case in Paxton Primary School.
We have over ten years of experience in MMC buildings providing both the detailed MEP designs and the building & energy modelling to provide full compliance.
We are leading experts in designing MMC educational buildings. Over the past ten years, we have designed over 100 MMC schools, which have recently been delivered via the DfE offsite schools’ framework. Examples for our educational MMC experience includes The Olive School, Collis Primary School, Whitehall Park Primary School, Paxton Primary School, Hollinwood Academy and The University of Edinburgh LRC
We have also delivered several complex healthcare projects utilising MMC, such as the world-class Translational Biomedical Research Centre for the University Hospitals Bristol NHS Trust. Our extensive experience in both the Healthcare sector and MMC buildings makes us uniquely placed to help you deliver your MMC healthcare project.